Smart Material Management in Construction: Tips and Tricks to Avoid Delays
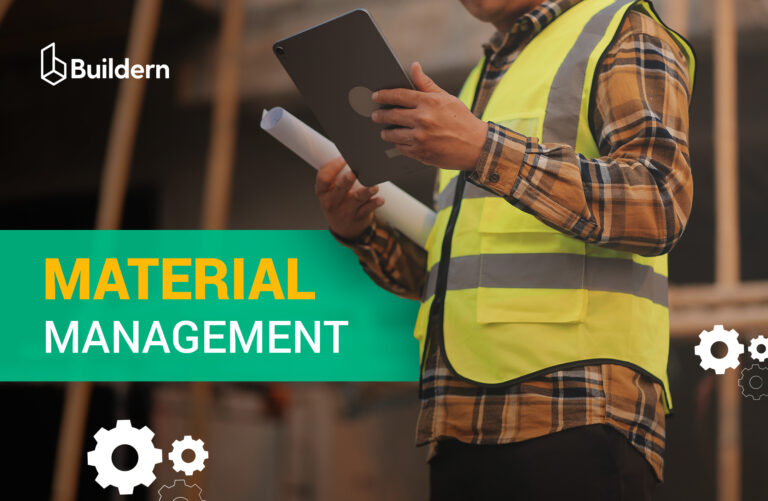
Have you ever ordered the wrong quantity of materials or tools? If so, you understand how poor material management can lead to costly delays and project budget issues.
Materials often make up the largest part of the construction project’s expenses. This is the reason material management is not only about logistics. It’s ensuring the right materials are available at the right time and in the right quantity to keep the project on track.
It’s essential to choose effective methods to manage the supply chain and plan the use of materials by subcontractors. In this article, we will discuss the smart methods of supply control at every stage of a construction project, from estimating to change orders and final delivery.
Table of Contents
- What Is Material Management in Construction?
- Who Is Involved in Material Management?
- General Contractor’s Role in Material Management
- Common Mistakes to Avoid
- Traditional vs. Modern Material Management
What Is Material Management in Construction?
It’s clear that regardless of the scope of a construction project, one cannot build without materials. However, just having them on site isn’t enough. A general contractor needs to have them delivered on time, stored properly, and used efficiently.
Construction inventory management and tracking affect every part of the project:
- Procurement: Sending bid requests and purchase orders to get the right materials from the right vendors.
- Delivery logistics: Scheduling shipments to the job site without clogging it up.
- Storage: Protecting materials from theft, damage, and the weather.
- Usage: Ensuring teams use the right materials at the right time with minimal waste.
Since this is a complex task, starting from estimating the quantity of any goods in the beginning and up to the delivery, procurement involves different teams.
Who Is Involved in Material Management?
Like any other effort in construction, it takes a coordinated team to plan and purchase materials effectively. Of course, this depends on project size.
Procurement managers/Material managers specialize in placing the orders, negotiating prices, managing contracts with vendors, and ensuring the timely delivery of goods in big construction companies.
Warehouse crews handle the incoming deliveries and track inventory. They manage physical storage of materials and are responsible for accurate record-keeping.
Field teams use materials daily and report on shortages of waste. In a big company, these could be supervisors and site engineers who oversee the handling and installation of materials. In a custom home project, this is a responsibility of a general contractor himself or a superintendent at the site.
Project manager keeps everyone aligned within the system. This includes coordinating procurement of the necessary materials at every phase of construction and communication with the field teams to keep the project on schedule.
Cost controllers or project accountants make all calculations and are responsible for the financial side of the procurement in a big construction project.
General Contractor’s Role in Material Management
Such a granular distinction of construction teams is usually typical for big projects. A role distinction in a small or mid-sized company can be different. A general contractor is often just one person who is dealing with procurement, warehouse supervision, or cost control.
A company may have a project manager who is coordinating the efforts. However, the general contractor measures the quality of needed goods, reviews the quotes, and writes estimates for clients or manages change orders.
How General Contractors Manage Materials Phase by Phase
Managing supplies isn’t one task. It’s a sequence of workflows that often overlap and require strict deadlines. Let’s break the workflow into phases that general contractors typically handle.
1. Requesting Bids
It all starts with sending a request for quotes during the project planning. Before a single order is placed, general contractors reach out to multiple vendors. In case of doing it manually, the process takes a lot of time. Imagine a home that is built from scratch. Hundreds of items are needed, from timber piles to tiles for the bathroom.
It’s not only about getting pricing, but availability, and delivery timelines for each material listed in the takeoff. This requires a clear way to organize vendor communication and track responses. Otherwise, a contractor may dig into emails and spreadsheets. With software management tools, it’s possible to automate the process. A building firm can keep supplier data, bid responses, and cost comparisons in one place.
Buildern, for example, enables a general contractor to link the bid request to the project schedule. When choosing a date, the system will show at what phase the inventory will be needed.
Without a full-scale procurement department, a general contractor is in direct contact with suppliers. Therefore, it’s important to get live updates within one platform.
In the case of software tools, there are built-in emails, an option to add attachments, or leave internal notes for the team. The same refers to discussing bid requests via messaging tools.
2. Estimating Project Costs
An accurate estimate is half of success. Material estimates are essential for planning and implementing the construction project as they directly affect the budget, schedule, and procurement timeline.
A clear estimate comes once the general contractor has as much information as possible from vendors. Now, when the best bids are assembled, it’s time to calculate.
An estimate usually includes quantities and unit costs with taxes, markups, and other overheads. This can be done manually or with the help of software to minimize manual entry errors.
Besides, when combined with software, it’s possible to create templates to save material estimates for new projects. Making adjustments is much easier than writing a new estimate from scratch.
3. Coordinating Purchase Orders
Once vendors are selected, the next step is putting together purchase orders. This is where planned quantities, unit prices, and delivery schedules turn into documents sent to suppliers.
A well-prepared purchase order includes detailed information about each item. There is a description, measurement, quantities, agreed prices, and most importantly, a delivery schedule.
Forming a clear PO ensures that every material request is clearly communicated and there is no duplication.
Here, major attention is on timing, especially when multiple vendors and trades are involved during project phases. Placing the right order at the right time can prevent early deliveries. Meanwhile, late arrivals also halt progress, and the project lags.
For example, imagine doors were ordered too early, weeks before they were needed. With no ready space to store indoors, it can be a real problem. Even if stored under a roof, the doors can warp because of humidity. This may lead to reordering, waste, and subsequently added costs to the project.
4. Tracking Delivery and Monitoring Inventory
In large-scale construction projects, it’s common to have a designated storage area. A special logistics team is responsible for deliveries and tracking inventory levels. They usually use barcodes, scanning tools, and inventory software.
However, it’s a different story for a general contractor working, for instance, on a custom home project. There’s rarely a dedicated warehouse or logistics crew. Materials are typically delivered directly to the job site. This makes the process tougher. The general contractor or a superintendent is the one who checks supplies.
Finding a reliable storage place may cause problems. A garage, basements, or secure containers may serve as a warehouse. This is why on-time purchase orders and communication with vendors are critically important. The materials usually should arrive as close as possible to the usage phase.
5. Dealing with Waste Management
Typically, the general contractor is dealing with waste management on the construction site. The builder coordinates handling of the construction debris, coordinates waste removal, and ensures compliance with local regulations.
The construction site should be safe, clean, and efficient not to pose a risk to staff. Sometimes the building firm delegates specific waste disposal tasks to subcontractors or specialized waste management companies.
6. Managing Change Orders
Changes may occur at any phase of a construction project. They are not always the result of any problem or miscalculation. A client may request a design modification, or some materials that were out of stock may become available.
A key task is to manage change orders in a way not cause delays or budget overruns. One of the biggest challenges is when changes of material or quantity do not fit the timelines. For instance, if a client decides to switch from laminate flooring to hardwood.
The replacement and return costs may take longer than expected. So, it’s better to use a universal platform that will have all the features in one to send change orders, receive approvals and rejections, and monitor the overall progress.
Common Material Management Mistakes to Avoid
Managing materials is not an easy task. Even experienced contractors can bump into issues. Here are a few issues to watch out for.
Too Early or Too Late Orders
The entire construction workflow depends on proper scheduling. If materials arrive too early, they can get damaged or even go missing. On the other hand, ordering too late can delay progress. Crews may be ready to start, but have to wait for materials to arrive, resulting in costly delays of the project.
Therefore, it’s so important to work with reliable vendors who have a track record of delivering on time. Besides, it’s important to plan purchases tied to the construction schedule.
Using construction software makes this easier. Tools like Gantt charts help visualize the timeline. If one phase gets delayed, material delivery dates can automatically shift as well. This kind of flexibility helps general contractors to have precise calculation details without having to reschedule everything manually.
💡 Coordinate material orders with a dynamic project schedule to avoid delays or early arrivals.
Inaccurate Takeoffs and Estimates
There is a high error risk for measuring material quantities manually during takeoffs. Besides, the prices, such as framing lumber prices, often fluctuate, which can impact overall construction costs.
A single miscalculation, a missed line item, or a typo can damage the material order. When using a software platform, the data flows directly into the estimate without manual re-entry of hundreds of items. This also means unit costs, taxes, and markups are calculated in one place, with much lower chances of error.
Another benefit of using software is the ability to include allowances. There is a big list of materials that haven’t been finalized yet before the project is launched. A client may make and change decisions on tiles or fixtures. Meanwhile, allowances help keep the estimate flexible even before decisions are finalized.
💡Take care of all details, including allowances, markups, and taxes, when planning the budget.
Poor Communication with Vendors
Misunderstanding between a general contractor and a vendor is also important for smooth supplies. Imagine a building firm sending a few emails to a vendor and not getting replies or calls on time. A delayed response to a quote request, missed confirmation on a delivery date is a problem.
Software tools offer subcontractor and vendor portals. Documents, quotes, and status updates are all in one platform. For instance, no messaging tools are needed to send photos of a material and receive a reply. All these functions are built-in, including the messaging function with a client to discuss a change order or other issues.
💡Choose clear and effective communication tools not to put construction at risk.
Traditional vs. Modern Material Management
Construction inventory management has always been a critical part of any project. However, the tools a building firm uses have changed dramatically. Traditional models rely on manual processes, while modern construction inventory software brings automation and easy solutions when tackling complex problems.
Construction Phase | Traditional Management | Software-Based Management |
Takeoff and Estimate | Manual measurements and calculations. | Automated digital takeoff; figures are automatically transferred to the estimate. |
Bid Requests | Sent via email or phone. Responses in spreadsheets, Word files, and notes. | Automated bid management with linked vendors, in-built emails and messaging tools. |
Purchase Orders | Created manually, often disconnected from project schedule. | Synced with schedules, clear documentation, and easy bill control. |
Inventory Tracking | Paper logs and manual checklists, risk of data loss. | Barcode or QR scanning, mobile apps, and real-time updates. |
Change Orders | Possible delays due to manual documentation and lack of visibility. | Transparent tracking, real-time updates, and online approvals in one platform. |
Vendor Communication | Emails, calls, and messages across different platforms. | Communication hub for vendors and subcontractors, built-in messaging and file sharing. |
Scheduling and Coordination | Schedule files in spreadsheets, and changes require manual work. | Created manually, often disconnected from the project schedule. |
Inventory management affects all phases of the construction process. Starting from the planning phase, it’s essential to ensure goods will be delivered at the right time and in the right quantity. This keeps projects on track and minimizes the risk of unnecessary expenses.
How Can General Contractors Avoid Material Delays?
The best way to avoid delays is to coordinate material orders with the construction schedule. Dynamic tools like Gantt charts and ensuring smooth communication with vendors help with inventory management. Software platforms can automate this process and adjust delivery timelines in real-time.
How to Simplify Communication With Vendors?
The right communication channels with vendors make the job easier. It’s better to centralize it and bring all messages and comments under one platform. Instead of emails, phone calls, and separate messaging apps, general contractors can use construction management software with built-in communication tools. Messaging and commenting features with quick access to files, like photos of the inventory, simplify the workflow.
What Are the Best Tools for Material Management?
Software platforms can minimize the risks of poor material management. Construction management software automates every step from scheduling to vendor communication. The precise figures and estimates are not lost when shifting from one construction phase to another. Having access to tools like Buildern, general contractors keep projects on schedule and within budget.