Construction Supply Chain: How Do You Manage It Properly?
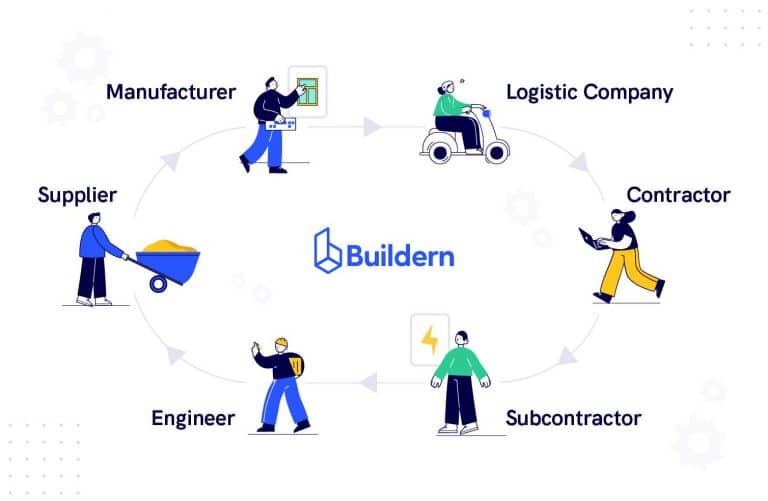
You have a construction project delay because of a material shortage.
Is it the internal issue of your team collaboration that resulted in late orders or the external issue of suppliers running out of stock?
Maybe the root of the problem is in the initial wrong takeoff that led to over or under-ordering materials.
Whatever the specific reason, the global issue lies in the inefficiencies of your construction supply chain management. One of the most complex processes in the construction industry, this engineer-architect-prime contractor-material supplier chain is the backbone of successful project completion.
If you don’t have a reliable system to manage it properly, you run the risk of material delays, unexpected costs, and, ultimately, project failure.
This guide will explore the ins and outs of construction supply chain management, providing you with best practices and tips to ensure your project runs smoothly.
What Is the Supply Chain in Construction?
A very simple way to define a supply chain in construction is as a series of interconnected activities to procure, manage, and deliver materials necessary for the successful completion of a construction project.
This includes everything from planning and sourcing to purchasing, transportation, warehousing, inventory management, and, finally, delivery to the job site.
A supply chain in construction is a more specific and detailed version of the general supply chain concept as it deals with the unique challenges and requirements of the construction industry.
Initially derived from the manufacturing industry, a construction supply chain is extremely complex and relies heavily on effective communication and collaboration between all parties involved.
The key reason is that too many players and processes are present in the chain, starting from the big-picture planning down to the smallest material details.
This includes not only the physical movement of materials but also the information flow between stakeholders – how much material is needed, when and where it needs to be delivered, and how changes or delays should be communicated.
A well-working construction supply chain ensures that materials are available when and where needed, enabling the project to progress smoothly and on schedule.
Who Is Involved In Construction Supply Chain?
Broadly speaking, everyone involved in a construction project is part of the construction supply chain.
Some of them, however, play more critical roles in the process than others.
- Suppliers are the key source of raw materials and components used to produce finished goods for the construction project. For example, a supplier may provide cement, steel, or wood to construct a building.
- Manufacturers convert raw materials into construction-specific products, such as windows, doors, or plumbing fixtures. They often work closely with suppliers to ensure the timely delivery of materials.
- Logistic companies facilitate the transportation and storage of materials from suppliers or manufacturers to the job site. They also coordinate with contractors to ensure on-time delivery and efficient routing.
- Prime contractors act as project managers, overseeing all aspects of construction supply chain management. They are responsible for sourcing materials, coordinating with subcontractors, and ensuring the project remains on schedule.
- Subcontractors perform specific tasks, such as electrical work or roofing, as part of the overall construction project. Their role in the construction supply chain mainly involves providing labor and expertise, for which they rely on materials supplied by others.
- Finally, architects and engineers play critical roles in the design and planning phase of a construction project. They work closely with prime contractors to ensure that the materials needed for their designs are available and delivered on time.
It’s extremely important to maintain a transparent and uninterrupted flow of communication among all parties involved in the supply chain to avoid delays and ensure successful project completion.
What Is Included in the Supply Chain?
We can also break down the components of a construction supply chain into processes and systems, where each step is essential for the overall efficiency and success of the project.
- As everywhere where the storage and quantity of goods are involved, inventory management is crucial in the construction supply chain. The main goal is to ensure there is no shortage of materials, as all needed items are restocked when they approach their reorder point. Also, the goal is possibly avoiding wasted materials, which can result from over-ordering.
- Quality control is the golden ticket to effective supply chain management, especially in the construction industry, where material quality can have a significant impact on project timelines and budgets. Quality control processes should be integrated throughout the entire supply chain, from sourcing materials to final delivery. This includes regular inspections, testing for compliance with industry standards, and clear communication about any defects or issues discovered.
- Demand forecasting or accurate prediction of the required data based on past performance, market conditions, and other factors also helps to optimize the supply chain process. The data-based approach to material planning and purchasing minimizes waste and avoids excess inventory.
What Is Construction Supply Chain Management?
The complex and multi-faceted supply chain process in construction requires effective management to ensure that all the moving parts work together seamlessly.
Construction supply chain management is the strategic planning and coordination of all activities related to procuring, managing, and delivering materials needed for a construction project. More sensitive part of the SCM is tracking and communication between all the players, coordinating schedules and deliveries, identifying potential issues or delays, and finding solutions to keep the project on track.
Without a centralized and properly coordinated supply chain management in construction, the chances are very high that the project will experience delays, increased costs, and decreased quality.
Why?
Because the flow of materials and information will be disjointed without an overlook on the whole process. Even one party’s delay or error can cause a ripple effect throughout the supply chain, leading to costly setbacks and disruptions.
That’s why one of the most effective SCM strategies in construction is bringing all supply chain-related communication into a single platform or system. This allows for real-time tracking and collaboration among all parties, reducing the risk of miscommunication or delays.
What Makes Supply Chain Management in Construction Hard?
Fragmentation is the number one factor that makes supply chain management in construction a challenge. Too many interdependent moving parts, each with its own processes, systems, and priorities, can create confusion and inefficiencies. Bringing different particles under a unified system and aligning them towards a common goal is quite tricky.
Global availability and sourcing of materials is another challenge. The constantly changing market conditions, availability of raw materials, and fluctuating prices often surprise the construction industry. As a result, uncertainty is always present in the supply chain, which can cause delays and disruptions.
Construction projects are also subject to various external factors: weather conditions, regulatory changes, or unforeseen events. For example, a sudden shortage of critical material due to natural disasters or global events can significantly impact the supply chain, causing delays and budget overruns.
Finally, sustainable procurement has become increasingly important in the industry. There is a need for transparent and ethical sourcing of materials, implementation of waste-reducing strategies, preference towards eco-friendly and recycled materials, etc. This approach can sometimes require significant changes in the traditional supply chain processes and systems because of the need to find new suppliers and adjust to different sourcing methods.
How Did the Pandemic Impact Supply Chain Management Issues?
Lockdowns, travel restrictions, and disruptions in global trade caused delays and shortages of construction materials. There arose new standards and requirements for worker safety, which had to be integrated into the supply chain processes. Additionally, the transfer of goods and materials falls under new safety regulations, which further complicates the complex supply chain.
Though the current world seems to have pretty much overcome the pandemic restrictions, the pandemic was a huge reminder that resilient supply chain systems are necessary for construction. Future planning should prudently take into consideration such unforeseen events when optimizing the supply chain processes.
Further in this blog, we discuss potential methods to do that.
Best Practices of Supply Chain Management in Construction
The more organized and centralized the supply chain is, the better all communication, tracking, and coordination are carried out, the less the risks of construction supply chain disruption. So, what are some of the best practices to follow in supply chain management in construction?
Let’s see!
1. Plan Orders Based on Forecasts and Historical Data
When planning orders of construction resources, the best hint is looking at how things used to be and what is predicted to be changed in the near future.
In more professional terminology, you need to look at your historical data for similar construction projects to take it as a base. Meanwhile, you should also look at trends in the construction industry, economic conditions, and market forecasts to create more accurate demand predictions.
OK, so how do you implement it?
First and foremost, ensure you have a robust data collection system that captures all relevant information about your past projects and performance. This can include materials used, project timelines, costs, suppliers, etc.
The only reliable way to do that is using construction project management software where you accurately record and keep all historical data and can easily access it when needed.
Below, you can see how Buildern stores detailed budgeting information for each construction resource, which can serve as a great reference in predicting future needs.
So, you can see which predicted and unpredicted expenses and material needs you had in your past construction projects and adjust your forecasts accordingly.
2. Establish a Reliable Network of Partners
We understand it’s easier said than done, but if you can leverage relationships with suppliers and contractors, it can be a game-changer for your construction supply chain management.
Having reliable partners means having fewer risks of delays or poor quality due to miscommunications or incomplete information about the project. Establishing long-term partnerships with suppliers and contractors can also provide cost savings in the long run, as they may offer discounts for loyal customers.
What we recommend here is bringing your bid requests and supplier data into one centralized platform, so you always have data to compare, contacts to reach out to, and historical information to refer back to for accurate forecasting.
Here is how Buildern stores all the offers that potential suppliers share with you.
And here’s a detailed list of all the payments you’ve made to each supplier, categorized by project or a specific bunch of materials.
Next time you order new materials for your new project, Buildern allows you to directly share the purchase order with the existing supplier in your database, making communication instant and smooth.
3. Enhance Collaboration Between Team Members and Suppliers
One of the “easier said than done” cases in the construction industry is keeping everyone synced. It’s hard when some of your project stakeholders are on the jobsite; others operate in the office. Additionally, there are suppliers spread across geographies and clients that need to be updated.
Again, a centralized system where all your data is stored and all communications are recorded and visible to everyone involved creates better transparency and helps avoid misunderstandings or delays.
With Buildern – an all-in-one construction project management software, you can easily invite any other project stakeholders to the platform and assign them specific roles and permissions.
Further, all parties see real-time updates on construction supply chain processes and can add comments or raise any concerns if needed.
For example, based on your granted permissions, certain team members can track your order statuses based on the shared purchase orders. Schedules and deadlines are also visible to all project stakeholders, and whenever any delay is foreseen or a change is required, all team members are instantly notified.
As Buildern is very user-friendly and has fully-fledged iOS and Android versions, all project stakeholders can stay connected and updated, no matter where they are.
4. Streamline Ordering and Billing Processes
As a general contractor, construction manager, or any other person who orders resources for a construction project, you can also cause a bottleneck in the construction supply chain.
This can happen because of ordering too late, ordering the wrong amount, or simply not keeping track of payments and invoices. If your vendors don’t get paid on time, they may hold up future deliveries of materials or even refuse to work with you in the future.
So, an integrated solution that syncs your construction project updates with your accounting/financing operations and stores all your invoices and transaction history in a single database is crucial.
If you work with Xero or QuickBooks, you can integrate them seamlessly with Buildern and import invoices and other accounting data in one click.
What does this mean for your construction supply chain?
- Once your order is delivered, you can quickly check it against all your made payments and see what’s due.
- Every transaction made with Xero or QuickBooks will be automatically updated in Buildern, allowing you to monitor your cash flow and expenses.
You can also use Buildern’s budgeting feature and check how much money you’ve allocated for specific materials or equipment so you don’t overspend.
1. Optimize Inventory Management
The whole construction supply chain management is about having enough materials and equipment in the right place at the right time without overspending or overstocking.
It’s also about proper storing of the ordered materials so nothing gets spoiled, lost or stolen, and you can always track the available inventory.
When we talk about optimized inventory management in the construction supply chain, the core component is ensuring that your orders always reflect the actual inventory. This means once a delivery is made or materials are consumed on-site, your records should be updated in real time.
Similarly, if some materials are returned to the supplier or you transfer them to another project, all these changes should be reflected in your inventory records as well.
If you can successfully keep track of all these actions in one place, the risks of overstocking or understocking are minimized, and you can save a lot of time and money in the long run.
2. Back Up Your Business with Contingency Plans
A contingency or reserve plan is something that most people think should be done in case of an emergency. However, when it comes to construction projects, having a contingency plan is not just a “nice-to-have” option but rather a necessity.
A contingency is a part of the construction budget that is put aside to cover unexpected costs that may arise during the construction process. These can be due to weather conditions, unforeseen design changes, material shortages, or other issues.
Having a contingency plan in place allows you to quickly address any problem without delaying the project or overspending. Additionally, it gives you more bargaining power with suppliers as you have a safety net in case of any delays or additional costs.
Furthermore, a contingency plan should also include a risk management strategy that identifies potential risks and has a plan of action to mitigate them. This is crucial for the construction supply chain as it helps minimize disruptions and ensures the smooth flow of materials and resources.
A 5-10% contingency budget is generally recommended for construction projects, but this can vary depending on the project’s complexity and other factors.
What Are the Benefits of Investing in Construction Supply Chain Management?
Investing in construction supply chain management = Ensuring smooth and efficient project execution
It also means you have tighter cost control, which is one of the most sensitive issues in the construction industry.
That should be your core reasoning to dedicate time, money, and effort to finding the right construction supply chain management solution for your business.
When you run small to medium-scale construction projects, you may not immediately feel the need for a comprehensive supply chain management system. However, as your business grows and you take on larger and more complex projects, managing the supply chain becomes crucial.
How Can Buildern Help Improve SCM?
Buildern is a consolidated source of every construction-related data, available to all project stakeholders at any time.
It’s a condensed source for different construction modules, including invoices, schedules, budgets, project progress, purchase orders, billing, and more!
There are two key benefits of integrating Buildern into your construction supply chain management.
- All modules are interconnected, and updates in any of them instantly reflect in the others. This means you don’t need to put extra effort into keeping different documents and systems in sync, saving time and reducing the risk of errors.
- For example, the budget and schedule modules will automatically reflect a change order on a project.
- It’s an extremely convenient platform for team communication and collaboration. It all consists of separate modules that operate with a drag-and-drop interface without any complex or hard-to-understand processes.
- Adding any comment or note, sharing files and other information with any team member is a matter of seconds. This leads to better coordination among project stakeholders, reducing delays and improving overall communication.
To Sum Up
For some reason, construction supply chain management is one of the most crucial yet underinvested areas in the construction industry. Quite often, companies invest a lot in advanced technology, tools, and equipment but overlook the importance of streamlining their supply chain processes.
However, an optimized construction supply chain is the cornerstone of a successful construction project. It ensures the smooth flow of materials and resources – something that is necessary for the construction project to complete on time and within budget.
If your business still relies on traditional methods of managing the supply chain, it’s time to consider investing in a comprehensive solution like Buildern. It not only helps optimize inventory management but also improves overall project execution and team collaboration.