No Penny Is Underlooked: 5 Types of Construction Cost Estimation
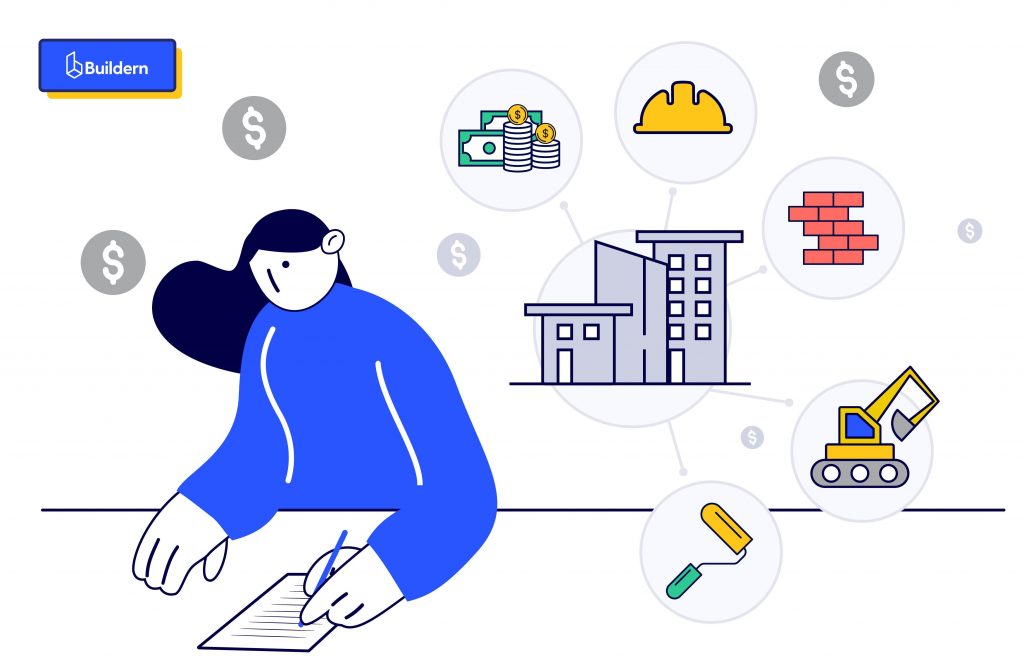
The wise construction manager knows that the actual cost of any project is only realized once the task is complete and all financial obligations have been accounted for. That’s because too many predictable and unpredictable factors can affect the cost of a major construction project.
Meanwhile, however challenging the task of predicting the total cost of a construction project may be, one thing is sure: estimating those costs correctly from the start is an absolute must.
With poor estimation, construction company risks veering from their bottom line as costs escalate, making it hard to make adjustments later on. It also makes it difficult to secure financial support and budget for the job.
Without proper estimation, contractors can’t determine which projects are worth pursuing and how much profit they can earn in the process. As a result, all parties involved in the project suffer.
That said, what steps should a construction manager take in order to estimate the cost of any given project accurately? This article gives an extended answer to that question by detailing the steps involved in construction cost estimation.
Read on to learn more about the process.
What Is Construction Cost Estimating?
Construction cost estimation calculates the total expected cost of any construction project before it begins.
Cost estimation includes all the components of a project, such as the labor, materials, permits, and other associated costs needed to build a new object. It goes beyond the initial costs and considers possible problems and adjustments that may arise throughout the project’s life.
Typical cost estimation comprises two main components: direct and indirect costs.
Direct costs are expenses related to the physical construction work, such as materials, labor, and subcontractor fees.
Indirect costs include items like taxes, interest payments, insurance premiums, permits, etc., which may not be immediately apparent but must be accounted for to determine the total cost of the project.
Usually, constructors provide owners with the estimation document, which includes an itemized list of costs broken down by component. In some cases, owners do not require the estimator to provide an itemized list, just the project’s total cost.
Once all the costs have been accounted for, a total estimated cost of the entire construction project is available. This is used to determine if it is feasible to pursue the project and serves as a guidepost throughout the job.
Estimation is an important and necessary step in construction planning as it helps set realistic expectations, secure funding, and gives stakeholders a better understanding of the overall costs involved.
Why Is Construction Cost Estimation Crucial?
Entering a construction project without properly estimating costs is a recipe for disaster.
Accurately predicting any job’s cost will help ensure that it meets the budget set by owners and other stakeholders involved in the project. It also allows contractors to accurately assess their profits and losses beforehand, helping them decide if taking on a given job is worth the risk.
Practical cost estimation also helps to plan for contingencies and prevent any financial surprises that could derail the project. It allows for more accurate resource allocation and identifies areas that require extra attention or where costs may have been underestimated.
Lastly, by analyzing the different components of a construction project, contractors can determine if they need to outsource specific tasks to experts or if they have the resources to complete the job themselves. This helps ensure that the job is done efficiently and with minimal disruption to the construction process.
That’s why it’s important that a thorough cost estimation is done before the start of any construction project. But how sure can you be that this process will be accurate and that the estimated costs will reflect reality?
Well, let’s see…
How Close Is Estimation to a Real Picture?
Estimating accuracy depends on the quality of information and data available to estimators. Furthermore, it depends on how well the estimator can interpret this data and make the necessary adjustments to account for changes in the market, inflation, or unexpected problems.
In other words, if estimators have complete and accurate information, they can estimate costs more precisely. It’s also crucial that they are familiar with local laws, regulations and building codes.
Of course, no one can estimate a project with 100% accuracy in such a complex field as construction. Weather changes, frequent cost fluctuations, and numerous other factors in the job site make construction one of the less predictable industries.
So, when we are talking about a good or an accurate estimation, we mean that an estimator accounted for as many factors as possible that could affect the construction process. A good estimation secures the project stakeholders from unexpected losses, which can happen if the expenses go beyond the budget.
The purpose of good estimation is to be as prepared as possible for issues that may arise and to be able to account for them in the project. It’s the base that allows contractors to set rational contracts with subcontractors and suppliers to get the materials needed for finishing the job without any financial surprises. It also helps contractors to set the right price for their services and to remain competitive.
At the end of the day, it’s important to remember that construction cost estimation is just that – an estimate. It should be taken with a grain of salt and used as a general guide for setting expectations, budgeting, and resource allocation during the project. If done right, it can help make construction projects run smoothly and efficiently.
When Should Builders Estimate the Construction Costs of the Project?
The sooner, the better.
Contractors should ideally begin estimating the costs of any job as soon as they have enough information. Once contractors know the size, scope and timeline of the project, they should get to work on calculating an accurate cost estimation as soon as possible. This will give them time to adjust their plans if needed and ensure they can remain within the agreed-upon budget.
The estimation stage should not come after the contract has started. Instead, it should be done before the project is awarded to ensure that all parties involved understand the costs and budget associated with the job.
No property owner will enter into a contract where they are unsure if their budget is realistic, and no contractor will want to be stuck with a project with costs beyond what the owner can afford.
Most construction proposals require cost estimation, as the contractor could not provide a realistic bid price without them.
5 Main Types of Construction Cost Estimates
There are 5 main types of cost estimations in construction, according to The American Society of Professional Estimators. These phases mainly differ in terms of the level of detail and accuracy, depending on the stage of the project and available data.
Here is a quick overview of each of the 5 main types of construction cost estimations.
#1 Order of Magnitude Estimate – Project Design Is Not Available Yet
The Order of Magnitude Estimate is used when the project design is not yet available. It is an early-stage estimate that provides a rough overview of the cost of the project, and it can help contractors determine if a project should continue forward or be pushed back.
This type of estimate is usually based on contractor experience along with available information about the project. It takes into account the scope of work, expected materials and labor costs, as well as any other factors that could affect the cost of construction.
#2 Schematic Design Estimate – Only the Schematic Design is Available
The Schematic Design Estimate is used when the project’s schematic design is available but the detailed design has not yet been completed. It takes into account more factors than an Order of Magnitude Estimate and provides a better idea of the construction costs.
The schematic design includes a basic layout of the project, such as the number and size of rooms and certain design elements. This type of design maps out the exterior, interior, and different structure systems, providing contractors with a more detailed overview of what resources they may need to complete the project.
#3 Design Development Estimate – The Initial Design is Available
The Design Development Estimate is used when the initial design of the project has been developed, and it takes into account more factors than a Schematic Design Estimate. It includes detailed information about materials, labor costs, and other factors that could affect the cost of construction.
This type of estimate requires contractors to dig deeper into the details of the project. It considers every element that could affect the cost and any potential changes that may need to be made along the way.
#4 Construction Document Estimate – Construction drawings are available
A construction document estimate is performed once blueprints and construction drawings are available. It considers all the details of the job, including the exact materials needed, labor costs, and any potential changes that may need to be made along the way.
Having construction drawings allows contractors to provide a more accurate estimate that factors in the actual size and shape of the building, as well as any other elements that could affect the cost.
This estimation phase can be considered almost final, as it is based on a detailed design and allows contractors to make informed decisions about the project.
#5 Bid Estimate – Construction documents are available
A construction bid estimate is the last step before the project is put out for bidding. It takes into account all the information gathered during the previous estimation phases and provides a detailed breakdown of estimated costs.
At this point, contractors have access to all the documents required for submitting bids and can make informed decisions based on the material and labor costs associated with each element of the job.
Bid estimates are used when bidding for projects and aim to provide contractors and investors with an accurate assessment of what the project will cost. The owner uses this estimate to compare different bids and choose the most favorable one for the job.
Before You Start the Estimate: A Bill of Quantities
Having a general understanding of the project cost is crucial before sending the proposal to the owner. That’s why contractors would normally create a bill of quantities – an itemized list of the materials and labor required for the job.
This bill of quantities provides a detailed overview of all the elements that will affect the project’s cost, such as construction material costs and labor expenses. It also allows contractors to make informed decisions about potential changes in order to reduce costs or increase profits.
Here are the main 4 steps that will help you construct an accurate bill of quantities.
Taking-Off Quantities
The term take-off in construction refers to the process of measuring the necessary material required for a project – the required quantities and cost of each material item.
Once the drawings are available, contractors need to start the process of measuring and calculating all the necessary items. Different quantity surveyors use different scaling dimensions from drawings. Usually, contractors use area, volume, length, et., to get the actual picture of the material items required for the job.
The outcome of this process is that the surveyor lists the material items and their quantities in detail.
Squaring
Once the initial take-off is ready, it is time to start the squaring process – a step that provides accuracy and allows contractors to double-check their calculations.
The key thing here is to ensure that all the material items are not only quantified correctly but also match the dimensions of the blueprints. This way, you can make sure that no mistakes were made during the take-off stage.
At the squaring stage, the surveyor multiplies the component’s dimensions into the square area of the property, then multiplies the result by the number of times the specific work happens during the project.
When this step is successfully completed, contractors get the total dimensions, length, volume and area of the project and can proceed to the next step.
Abstracting
So, you have all the measurements and quantities in one place. Now it’s time to move on to abstracting – a process of grouping material items by similar types so that they can be easily identified during pricing and bidding.
The goal here is to create a set of standardized bills, which will help you avoid any confusion when preparing for the bidding process.
Abstracting requires a detailed approach; it includes combining similar tasks and components together. By merging them, surveyors can create a list of items that require similar pricing measures.
Billing
The final step of the process is billing. As simple as it may sound, billing is the process of presenting the results of the previous steps – surveyors present item descriptions and quantities in a structured format which is called a bill of quantities.
A bill of quantities serves as a basis for a contract, and thus it needs to be detailed and precise. This is why it should include all the necessary information regarding the project’s scope of work – material descriptions, quantity breakdowns, labour costs, etc.
The goal here is to ensure that all the material items are properly priced and accounted for before submitting the bid. Contractors usually use itemized pricing, which also allows them to identify potential savings or areas where costs can be reduced.
Altogether, the above steps – taking off, squaring, abstracting and billing – prepare the base for an accurate construction estimation. It is a detailed document that helps contractors understand the project’s scope, cost and labour requirements better – all while avoiding potential mistakes.
Which Components Go Into Construction Cost Estimate?
Before we list the main construction estimate components, it’s worth noting that construction estimation for different projects can vary. This is why it’s important to adhere to the specific requirements of your project and include all the necessary elements in the estimate.
With that said, here are some of the most common components used during construction cost estimation.
Labour Costs (Hour and Rate)
Labor costs comprise around 50% of the construction project, so this element is crucial to the estimate. This number should include both the hourly rate and hours required for each employee, including skilled and unskilled workers.
To accurately assess required labor costs, estimators need to consider the complexity of each task and include separate entries for various employee types.
To clarify the estimate for your client, separate all the labour costs and associated elements, like overtime or bonuses. Give a clear picture of who will work on the jobsite, for how long and at what cost.
Materials
Estimators already have an estimated cost of all the required material from the take-off process. This includes everything from construction equipment to raw materials and tools, which should be present in the bill of quantities.
If any additional items weren’t originally included in the list, estimators need to include them separately and adjust all the pricing accordingly.
A crucial tip here is to leave space for a potential increase in material costs, as prices can vary significantly during the project. Materials prices are often subject to fluctuations in the construction industry, where projects usually last for more than a year. Meanwhile, contractors can’t stockpile all the construction materials in advance, so the cost fluctuations don’t affect the project cost.
So, however challenging the prediction of material price fluctuations may be, estimators should always make sure to include this element in the construction cost estimate.
Equipment
The equipment section should include any cost associated with owning or leasing construction equipment, as well as costs of transporting and securing the equipment.
In some cases, it may be more rational to rent equipment instead of buying it. Depending on the size of your project, it can save a lot of money in the long run – which is why estimators need to include all the possible options when deciding on the type and cost of construction equipment.
Leasing equipment is usually a good choice when the construction site is far away from the company’s location, and transportation costs will outweigh the rental costs. It’s also a good choice if the project requires specialized equipment, which will not be used often for other projects of the contractor. In this case, as compared to buying it, renting will be much more cost-efficient.
Subcontractor Quotes
In some cases, estimators need to include subcontractor quotes. These should include all the necessary labor and material costs associated with the subcontractor’s project work. If you’re going to outsource a part of the project to another contractor or subcontractor, make sure to do thorough research and choose a reliable subcontractor that will cover specific parts of the project. Further, there should be clear agreements with the subcontractor regarding the timeline, payment and quality of the work, as you will plan your construction contract based on the subcontractor’s estimate.
An important tip here is to ensure that you initially receive a quote from your subcontractor, which includes both labor and materials. This helps avoid any potential cost overran later in the project.
In this regard, building a solid network of subcontractors you can trust and rely on is crucial. With a reliable network of subcontractors, this section of your construction estimation will be more predictable and easier to manage.
Indirect Costs
Construction is not only about materials and labor but also about the additional costs that go along with it. This includes anything from fees to taxes, insurance and administrative fees.
Indirect costs can add up quickly, so estimators should take their time assessing them and ensuring all the expenses are appropriately listed in the construction estimating document.
If you miss indirect costs during the estimation process, it can lead to significant budget overran later in the project. This is why you need to keep track of all the additional expenses and ensure they are properly accounted for.
Escalation
Escalation in construction is the increase in cost due to inflation, currency fluctuations or other market factors. It’s important to account for this element in your construction estimation document as it can significantly impact the final project budget.
An escalation component in your contract secures you from budget overruns, implying that if prices rise, the project cost will still be covered and contract terms will be adjusted.
Capital Costs
Capital costs are investments made in the early stages of a construction project and are planned to benefit the project for more than one financial year. Depending on the contract, some of these costs may need to be included in the initial construction estimation.
For example, capital costs can include purchasing a new crane or investing in a property that will later be used as part of the project.
Bonds
Construction bonds are insurance policies that guarantee the fulfillment of contract terms and secure both parties from financial losses if the project doesn’t run according to the predetermined schedule. Depending on the scope and size of the project, it’s important to include bonds in your construction estimation document.
The bond amount may depend on various factors such as the type of contract, duration of the project or even weather conditions at some point in its implementation.
Operations
Construction operations include the key activities happening on the construction site. Examples are measurements, cuttings, welding, post-construction cleaning and other activities. All these need to be accounted for in the construction estimation document so that it’s clear what needs to be done and how much it costs.
By including detailed information about operations in the estimation document, you can ensure that all the required activities are accounted for and that there won’t be any surprises later in the project.
Variances
Variance in construction is the difference between a project’s estimated cost and its actual cost. Though the variance can’t be predicted with 100% accuracy, estimators should build some extra margin into their estimates to account for it.
This will help reduce the impact of potential cost overrun and ensure that the project is completed on time and within budget.
Contingencies
Contingencies are allowances built into the construction estimation document to account for unforeseen expenses during the construction. In other words, it’s an extra budget that can be used in case something unexpected happens and you need to buy additional materials, hire more people or make other unplanned expenses.
An industry standard for risk contingency is 1-3% of the project’s hard costs. However, depending on the mutual agreement with the owner, you can also adjust the contingency amount, including some percentage of soft costs as well.
A contingency reserve can also pay contractors extra incentives or bonuses if the project is completed on time and within budget.
Profits
Last but not least, don’t forget to add a profit component to your construction estimation document. It’s important to ensure that after all expenses are paid, you still get a fair return on investment for the services and effort provided during the project.
The profit component should be discussed with the owner before finalizing the contract and it may include a percentage of total costs or a fixed fee. The bottom line is that both parties should be on the same page regarding how much profit will be made at the end of a construction project.
Fairly New Concepts in Construction Cost Estimates
Construction estimation is not a static process, as new technologies and ideas are constantly coming onto the scene. Recently, new concepts such as BIM or LEED Certification have been added to the list of factors that need to be considered when creating a construction estimation document.
However, that’s not accepted as a norm yet, as many argue that these new concepts can decrease the reliability and accuracy of cost estimation. Anyways, here are some of the newest trends in construction cost estimation that you might want to include in your scope of work.
Building Information Modelling
BIM or Building Information Modeling is an advanced digital tool used for creating 3D models of actual buildings in order to manage and plan construction projects. Ideally, BIM Models should accurately reflect all the dimensions and elements of a building, which can help estimators better understand the scope of work and make more accurate estimates.
Pros: If there is a chance to have all the construction data without digging into blueprints, it can save time and costs.
Cons: Some estimators don’t trust BIM to reflect all the details of a construction project, so, according to them, it can’t be trusted as a sole forecasting tool.
LEED Certification in the USA
In the era of increased requirements toward sustainability, many owners require their buildings to be LEED certified. This means buildings should correspond to specific energy efficiency standards, water usage and other environmental requirements.
If the construction project is to be LEED certified, it’s important to include the necessary expenses in your estimation documents. Those include direct and indirect costs.
In LEED projects, materials should be selected carefully to make sure they meet the requirements. In this case, material affordability takes second place, and the key factor is the materials’ environmental impact.
Besides direct costs, LEED-certified projects add administrative costs to the construction estimation, as there is a need to prepare additional paperwork, meet certain inspections or advice from certified professionals.
Note: A company that operates in Australia must obtain Green Star certification. Sharing the same conceptual approach with LEED certification, it suggests that construction companies must build sustainable buildings for the community.
Lean Construction
Lean construction is a concept derived from lean management, which intends to reduce waste continuously in terms of time and resources while maintaining the same productivity. This can happen by identifying activities that don’t add value to the process and eliminating them from the project activities.
This approach can help reduce costs significantly throughout the entire construction process, as it focuses on decreasing rework, optimizing workflow, etc. If a project is going to be done based on lean principles, then this should be included in the construction estimation documents.
In other words, if a construction estimator is familiar with lean principles and knows how to apply them throughout the project, the estimations should reflect the potential savings that lean construction can provide.
Though those principles are not yet an integral part of any construction cost estimation, the complexity of modern construction projects calls for new ways of estimating. Keeping your eye on the newest trends in the industry can help you stay ahead of the game and make your estimates more accurate.
3 Main Estimating Approaches
Here’s how you can approach the construction estimation process:
Unit Pricing
Unit pricing is best for estimating direct costs, which can be easily measured and compared, such as materials and labor costs. To estimate a construction project with a unit pricing method, you need to have a library of specific unit costs for each element.
These are called Cost Codes and help construction industry players easily identify different materials and labor costs. So, 01 are General Requirements, 11 are for Equipments, and so on.
For unit pricing estimation, the contractor must have a particular element’s required quantity during the construction project and unit cost to make the total estimate. For example, if a contractor needs to know how much it’ll cost to build a 3-meter wall and knows the unit cost of the 1-square foot wall is $10, then they can make an accurate estimation.
Square Footage Pricing
The square footage pricing method is a dirty estimate approach. It means the estimator should use the most basic calculations based on the square footage of the built project and then add a percentage to that to account for additional costs. In this case, the estimator uses the total floor area or building size as the base number and adds some percentage based on previous experiences.
This is a fast and easy approach for rough estimation that does not require much work on the contractor’s side. This method is often used when there is a need for quick proposals and contractors do not have enough time to do an in-depth analysis.
After the rough estimate, contractors and owners get into detailed discussions, and more accurate estimations are made. So, there is no need to be afraid of starting a project without a detailed estimation and then experiencing financial losses.
The Rule of Two
The Rule of Two is based on the idea that labor costs account for around half of construction projects. So, if contractors can roughly estimate the man-hours needed for the project, they can double that number to get a rough estimation of the total costs.
For instance, if a contractor suggests it takes 10 man-hours to complete a particular task or group of tasks, the estimated cost will be twice as much (20 man-hours).
However, there should also be a profit margin and some reserve budget in case of unexpected costs. This number is usually 10% of the doubled labor costs in the Rule of Two methods.
The Easiest Way to Estimate Construction Costs: Try Buildern Now!
Investing in modern software solutions is a wise way out if a builder lacks specific resources or skills while estimating a construction project.
Clear and concise construction cost estimates are the essential ingredients of a successful project. Buildern is designed to help construction industry players track, measure, and estimate project costs effortlessly.
It comes with essential feature packs providing its users with a centralized system for construction project management.
Let’s see how the platform deals with construction cost estimation:
Step 1. Define Your Main Estimating Approach
Whether square footage pricing or the rule of two, having a clearly defined strategy defines your future success. Buildern effortlessly integrates with major accounting platforms Xero and QuickBooks.
Thus, assigning costs to categories for later analysis is easier and requires less effort.
Step 2. Cost Estimation in Preliminary Budgeting
Once you add overheads, local taxes, insurance rates and other project-related cost data to your professional dashboard, Buildern will use them to help you make a preliminary budget.
Accurately estimate the cost of a construction job with the help of Buildern’s budgeting module. The platform allows users to estimate preliminary project costs quickly and efficiently.
Step 3. Estimating Labor, Materials, and Equipment Costs
Provide your client with a detailed representation of materials, man-hour rates, equipment costs and everything you’ll need to estimate accurately. Buildern allows you to quickly break down the costs based on their components and make necessary adjustments.
Construction budgeting is the fundamental step in any construction project. With the help of Buildern, you can accurately estimate and manage your investments to ensure a successful outcome. While different methods are used for cost estimation, finding a supportive tool to guide you along the journey is the key to success. Try Buildern for easy, accurate construction cost estimation today!