What Is Construction Takeoff and How to Do It?
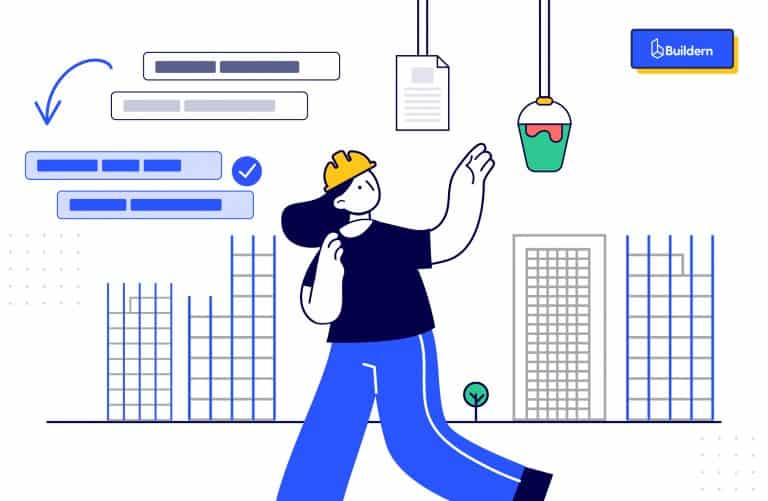
Let’s put it straight. How many times have you struggled to estimate a construction project? It’s an unpredictable field, and it takes more than a gut feeling to forecast materials and the overall project budget accurately. That’s why construction takeoff is so essential; it allows you to plan, predict the number of materials needed for the job, and ensure that you don’t run out of supplies.
It’s no secret that materials account for the largest portion of construction project costs. Mastering takeoff will become your ace in the hole to stay successful in the long run. Estimating takeoff doesn’t have to be an experience of dread. By using takeoff software and following the proper estimating techniques, businesses can control their project and ensure that everything is finished on time and within budget.
We’ll further guide you through takeoff construction principles and teach you to evaluate takeoff estimates so that you can confidently plan your future construction projects!
What Is Construction Takeoff?
The term takeoff construction, also known as quantity or material takeoff, refers to extracting a list and quantities of materials involved in a construction project. The process implies calculating the total materials needed to complete the project. Takeoff estimations might include the following:
- Lumber broken down into specific numbers and types (e.g., 4×4’s, 2×6’s, etc.)
- Drywall
- Concrete
- Windows
- Insulation
- And any other materials required to complete a construction job
View it as a draft for the construction project—a starting point to begin planning the entire task. When you master construction takeoffs, you can ensure accurate estimations and have the upper hand when bidding for a new project. A business, thus, gets the opportunity to maximize profits and stay competitive in the market.
An accurate takeoff enables general contractors to produce precise and reliable estimates, forecast the budget accurately, and price out competitively. Using takeoff software and following the proper estimating techniques, calculations can be done faster and more accurately than ever.
How Is Construction Takeoff Different From Estimation?
Although construction takeoff and estimation may seem similar at first glance, there is a subtle difference between them. Both notions are essential in the construction and are used to calculate project costs.
However, takeoff is a preparatory step for creating an estimate. Dealing solemnly with material management, takeoff focuses on the materials required to complete the construction project.
Estimation is the overall process of calculating the project cost based on extended takeoff listings, including labor, overhead, and other factors. It’s the exact amount that you would charge the customer for your services. It’s a wide-ranging stage that deals with all aspects of construction project management. Estimation takes a simple takeoff further and involves assessing it, evaluating the risks, and optimizing pricing.
Why Perform Takeoff If There Is a More General Process of Estimation?
Here’s a dilemma.
If the estimation is a more comprehensive process, why use takeoff?
It’s hard to disagree that construction takeoff requires considerable time and effort. It’s a complex practice, including precise calculations, deeper professional insights, and the ability to predict future obstacles.
Still, the answer is simple: construction takeoff allows you to forecast the total cost of materials more accurately and eliminate the risk of running out of supplies. With an accurate takeoff, it’s possible to create a reliable estimate – the heart and soul of project success. As takeoffs help construction companies win contracts by giving them the confidence to provide accurate estimates, these are the basis of your future estimation to help you stay competitive.
Takeoff software allows contractors to plan ahead, quickly break down prices of materials needed for the project, and optimize their costs. As a result, you can provide your customers with accurate prices and reliable estimates without going through hundreds of paper calculations.
Thus, keep in mind that takeoff is critical in construction project management as it creates a solid base for precise and professional estimates. Mastering construction takeoff will make an unrivaled competitive advantage in your construction business.
Who Should Perform Construction Takeoff?
As a rule, general contractors and subcontractors are in charge of having decent knowledge and skillset regarding project management and estimating. Skills to accurately evaluate construction plans and drawings, estimate construction materials, and apply a competitive price structure are necessary for those who want to succeed in the sphere.
As a rule, takeoff estimators act as a bridge between the sales and production teams. They are usually in charge of collecting, organizing and analyzing construction plans. Takeoff estimators can help you streamline the entire contract bidding and evaluation process, allowing you to compete with more established companies in the field.
Thus, takeoffs should be an integral part of the estimating process for any company striving to grow and prosper. With it, you can make the unpredictable construction business more controllable and ensure that every project is finished on time and within the set budget.
What Is Included in the Construction Takeoff?
As we already know, takeoff includes all the materials, raw and added manufactured fixtures, and other construction components required to complete the project. That said, there is nothing else to add. Nevertheless, let’s quickly skim through each group of materials necessary for precise calculations.
Raw materials include the so-called construction staples like wood, bricks, metals, concrete, clay, etc. These are essential construction elements used in projects of any size.
Added manufactured fixtures consist of all the items produced by the manufacturing industry and consumed during construction works. Examples are construction tools, nails, insulation, plumbing and electrical fixtures.
Lastly, any construction project requires additional components like paint, drywall, roofing and flooring materials. These construction elements are generally purchased from either a wholesaler or a retailer.
Construction takeoff allows construction companies to accurately predict the number of materials used in their projects and make sure they don’t underbill or overbill their clients.
Four Key Types of Measurements In Construction Takeoff
Count, length, area and volume are the key measurement types used in construction takeoffs. Each has unique rules and functions that construction estimators use to assess project plans.
Count
The count type measures the number of items in a construction project. This could be anything. For example, construction estimators may use it to estimate the number of bolts and construction staples needed per project.
Although it may seem a waste of time, count measurements are essential for any construction takeoff, as they provide an accurate picture of the number of materials needed to complete the project. Overbilling clients for an unnecessary amount is something to avoid.
Length
Materials with linear measurements require precise length calculations. This could include construction staples like lumber, pipes, wires, cables and other components with a constant linear measurement. Builders need extra measurement equipment and software to accurately estimate the length of these items.
Another use case is measuring the staircase, decks or any other construction item with a linear shape. Measuring walls and complex systems can be harder and requires additional equipment.
Area
The area type is used to measure construction elements with a two-dimensional measurement. It means that construction estimators must factor in the length and width of such elements. For instance, using area measurement applies to flooring, cladding, the amount of paint for a given surface, etc.
Volume
Finally, construction estimators use volume to measure materials like asphalt or concrete. This type of construction takeoff is far more complex than the other three types since construction estimators need to factor in length, width and depth when making their construction takeoff calculations.
Although all calculations require double attention and extra effort, construction estimators must pay extra attention when measuring volume. This is because the measurement of volume can be significantly affected by the shape of the construction element.
Calculations for Different Materials
With so much material, data, and details to include, contractors must understand each material and how it works in construction projects. Furtherly, we will discuss several handy techniques to help you handle calculations for raw materials, manufactured fixtures and materials for flat surfaces.
Calculating raw materials: Consider including the precise dimensions before incorporating raw materials into takeoff calculations. Include the height, depth, width, weight and everything you consider worth mentioning. This will help construction estimators make precise predictions regarding materials needed and construction costs.
Calculating manufactured fixtures: Estimators coping with such construction materials must factor in the construction specs according to their local standards. As a rule, the takeoff should include the estimated quantity to provide accurate prices.
Calculating materials for flat surfaces: For instance, roofing and tiling materials help create flat surfaces in construction. Estimators need to rely on area measurements for the takeoff of the space rather than the dimensions.
Analyzing and making precise calculations help contractors accurately predict and control future costs while giving them a complete overview of every construction element.
Which Costs Go Into Construction Takeoff?
We know that the volume of materials is the direct construction cost. However, construction estimators also need to factor in the current and future price changes. Price fluctuation can cause final cost changes, so it is crucial to consider the estimated lead time of construction materials and equipment.
Future cost increases impose significant challenges to any project management, as contractors must decide on a working strategy to pass the costs onto the clients. The process requires proficiency and market knowledge to give them the best chance of keeping the project within budget. Moreover, the ability to forecast future trends and forces that may affect the cost of materials and equipment is a valuable asset.
How to Perform Construction Takeoff? Manual and Digital Methods
To make construction cost projections, you have two essential methods: manual and digital. Choosing one may be challenging, as both have pros and cons. Let’s break it down for a clearer understanding.
Manual construction takeoff is suitable for small-sized projects as it implies composing a list of all materials and measurements without additional advanced tools. The main disadvantage is its time-consuming nature, as contractors must manually enter the data. Plus, there’s no margin for error since all measurements must be precise.
Digital construction takeoff is a far more advanced method and requires specialized software. It helps contractors save time since the measurements are done automatically. Plus, the software helps budget estimation and allows cross-referencing between labor and material costs. The downside is that some takeoff software is expensive and complex, making it challenging for beginners.
You can make informed decisions and accurately manage your projects when you understand how the process works. That’s why we will furtherly examine both methods more closely.
Manual Method
Pen and paper are the crucial tools estimators need to utilize conventional takeoff. The process includes measuring the exact dimensions of the space and recording all materials used in the project.
Estimators work directly off a physical blueprint and must be aware of the precise dimensions and quantities, as it helps them calculate costs. As a rule, manual takeoffs imply using complex mathematical equations to calculate materials and time. Depending on the scenario, estimators may also need to factor in the thickness, weight, and height for total accuracy.
A clear understanding of the symbolic language used in blueprints is also necessary as it helps estimators accurately interpret the diagrams and determine which materials are suitable for specific projects. Diagram representations of the electrical or plumbing layout are also essential. These should contain symbols and notes indicating the location of outlets, electrical boxes, drainpipes, and other objects.
While manual methods require greater analytical and mathematical skills, they need more time and effort than digital ones. Still, they tend to be cost-effective and suitable for small or medium projects.
Why Is Manual Takeoff Becoming Outdated?
Although manual takeoffs are a popular method in many industries, digital strategies are slowly becoming the go-to choice for most estimators. The downsides to manual methods are gradually becoming apparent, as they’re time-consuming and vulnerable to errors.
First, manually reviewing blueprints and gathering accurate measurements is a tedious process and can be prone to human error.
Secondly, the manual method tends to be limited in analyzing data efficiently. This can lead to discrepancies in the estimations and make it challenging to produce a detailed price list of materials.
Lastly, manual methods need to be better suited to scale up the estimating process, and they can use data from past projects. This means that estimators must manually review every project and calculate costs from scratch each time. It can be incredibly time-consuming when a project is substantially large or complex in nature.
Although manual takeoffs can seem cost-effective for smaller projects, digital methods are more reliable and will save you more time and money in the long run. Let’s furtherly dig into digital strategies and see how they help construction companies leverage their estimating process.
Digital Method of Construction Takeoffs
Although manual approaches continue to be popular, there is a growing demand for digitalization. With the right software, managers and estimators can streamline their estimating process and master construction time management.
The digital approach significantly decreases the time spent on calculations. Not only does it eliminate the need for manual measurements, but it also allows estimators to quickly and accurately review dimensions. Moreover, advanced technological guidance requires lower expertise with smaller learning curves.
Digital methods are convenient when estimating large construction projects. For instance, a platform like Buildern allows estimators to generate a detailed list of materials for any specific project. Having everything at hand and calculating costs instantaneously will enable estimators to see the whole real-time picture and reduce the chances of errors.
The method proves more convenient as the takeoffs are generated directly on the digital blueprint with software. Directly entering information into a digital system prevents any discrepancies resulting from data transfer.
Moreover, such advanced systems can integrate with third-party applications to view the bidding, purchase orders, paid and pending invoices, and other related information. Digital construction takeoff methods offer a wide range of benefits to the estimating process that manual ones cannot match.
Why Use Software for Construction Takeoff? 4 Benefits You Cannot Miss
Digital takeoffs imply having a professional, up-to-date software solution to create more detailed estimates. This allows managers to generate a completely accurate list of materials and related costs.
Thanks to modern advances in software technology, digital takeoffs are far more advanced and accurate than traditional manual takeoffs. If saving time and providing the utmost attention to details are your company’s top concerns, the future of construction takeoff lies with digital methods.
In a nutshell, here are the four main advantages of using software for construction takeoffs:
Saving Time for Estimators
Digital takeoffs are incredibly time-efficient. By eliminating the need for manual measurements and entering data directly into a digital system, digital platforms keep every detail under control.
Whether the project management requires counting fixtures, calculating quantities and costs, or simply reviewing dimensions – everything becomes quicker with the help of software solutions.
For instance, Buildern’s real-time cloud-based library management allows the teams to access the most recent drawings, files, and other construction-related documents at any given moment, reducing the risk of errors or discrepancies.
Higher Accuracy
Digital construction takeoff ensures estimators a greater level of accuracy than manual takeoffs, as they are not prone to mistakes. It all depends on the ongoing data and calculations, which are all handled in real-time.
Modern software solutions provide accurate takeoffs for any given project within minutes. Using the inputs of the construction plans and blueprints, estimators can precisely check every detail. Whether it’s preliminary budgeting or a detailed analysis, having a professional helping hand will guarantee the utmost accuracy and prevent any potential miscalculations.
Increased Efficiency
Construction management is known for its unpredictable nature, making it difficult for construction companies to plan their projects. Storing pages and pages of information and cross-referencing it manually can be a tedious and time-consuming task.
Using a digital platform for construction takeoff allows teams to perform more estimates in less time. In its turn, this means faster bidding and higher profitability.
Minimizing time spent on the estimating side of the project means having more time to focus on the actual construction.
Competitive Bids
With all the advantages of digital takeoff, it’s no surprise that construction companies can stay ahead of the competition. A precise bidding process is a must in this industry, as it grants them the ability to win projects and increase their revenue.
While digital construction takeoffs eliminate the risk of human error, they also help estimators determine quantities and costs and present them in a much more organized way.
Using digital platforms for construction takeoff can save estimators and construction companies time, increase accuracy, create efficiency and competitiveness, and help them stay ahead of the game. Considering all these benefits, software for construction takeoff is undoubtedly essential for any contractor wanting to upscale their business to higher levels.
That said, let’s now switch and learn about the breakdown and main steps a construction estimator needs to go through to create a competitive takeoff.
Construction Takeoff Process Breakdown | 4 Key Steps
While every construction takeoff project is different, there are four main steps that every estimator should follow. We’ll break them down one by one outlining the key objectives of each and how they can be achieved with advanced tools.
Step 1: Carefully Examine the Project
The beginning is always the most responsible part of any project, and construction takeoff is no exception. Estimators must carefully review the construction documents, such as blueprints and plans, to ensure they understand what is needed correctly.
Also, consider discussing every little project-related detail with the client, including their budget and timeline. Doing so will ensure the estimator includes all necessary information in their takeoff, meeting both the client’s expectations and legal requirements.
The first step requires accuracy and attention to detail as it will define the entire workflow. That’s how a construction project management tool can come in handy. Buildern offers users a unified platform with advanced tools and features to optimize preliminary takeoffs and more extended estimates.
A professional dashboard is key to smooth communication and collaboration within the team while all the data is stored in one place. Leveraging such a platform will reduce manual paperwork and help you prioritize activities accordingly.
Step 2: List Down the Required Materials
The second stage of construction takeoff breakdown implies listing the required materials without quantities and prices. View it as a draft of the whole project. Ensure you include any extras or additional materials that might be needed once the project is in progress.
Due to automated integration, you don’t need to add each item and its details manually. Instead, you can quickly access the database of materials and select the ones necessary for your construction project. Again, a digital platform or an estimating software API can significantly help.
Buildern has an easy-to-handle dashboard for construction project managers and general contractors to add their corporate cost codes or use the internationally accepted ones to identify each item.
Buildern allows inserting all project-related data into your project’s dashboard, thus, opening access for chosen team members. They will either view project details or adjust them accordingly. With such software, estimators can securely store all the information and documentation, review it as often as needed, and be sure that all data is safe and up-to-date.
Step 3: Estimate the Required Quantities of Materials
Once you clearly understand the upcoming project scopes and materials necessary, it’s time to focus on the quantities. Measurement accuracy is essential here as the project budget will depend on the estimator’s accuracy.
Of course, depending on the project size and duration, manual takeoff can solve a few key issues. Nevertheless, the best approach will be implementing automated measurement takeoff tools that allow estimators to select certain blueprint areas and quickly calculate their area or the number of materials needed.
In Buildern, you can use the Estimate tool to represent the required quantities and prices professionally. With the already listed cost codes and materials listed on a separate dashboard, creating a takeoff is straightforward.
Use your preferred measurement system and ensure you cover all the expenses. While the takeoff should only include costs and quantities of the materials used, Buildern users can extend the scope and create more detailed estimates.
The process is pretty simple:
- Create a project. It’s the first step toward opening a unified working dashboard that will include all essential data concerning your project. Managers will find all the paid and pending invoices, the estimated construction costs, and the progress schedule.
- Enter the estimate feature. Here you will be required to add the necessary materials, cost codes, and other details that will shape the project’s future takeoff and the final estimate.
- Assign to the corresponding project members. Buildern has a handy feature to define specific roles and permissions for each team member. This way, you’ll keep everything organized and ensure the tasks are completed on time.
Step 4: Determine the Costs
The last but not least step is to calculate the total cost of a construction project. Estimators must set up their desired profit margin and the prices they will charge the client.
As construction takeoff and estimate require complex mathematical calculations and precise data about each item’s price, the best way to ensure accuracy is by using a digital tool. Buildern controls your project’s budget with advanced algorithms and an intuitive dashboard.
Several factors may affect the total cost of a project. For instance, unexpected delays, labor costs, suppliers raising prices, etc. With Buildern’s accurate construction takeoff, estimators can anticipate these factors more efficiently and ensure the budget is kept in check.
Although this is the final step on today’s list of critical project management breakdowns, estimators must note that depending on the project type and duration, each step may have additional substages. Buildern is the most reliable construction takeoff software that easily tracks your project’s progress, costs, and materials. Even if you urge to adjust the budget and the pricing plan during the project’s lifetime, the software will make the process as smooth as possible.
Conclusion
The struggle to estimate a construction project and provide transparent budgeting reports is an absolute nightmare for many construction companies. It’s a field full of underwater stones and many potential risks.
Though, with the proper construction takeoff software, estimators can get a detailed overview of their project’s costs and materials required. It’s the first step to efficiently controlling a construction budget and being transparent about the costs and spending.
We now know that preparing a comprehensive takeoff procedure is essential to ensure success and outline your company’s proficiency. As manual takeoff relies on paper plans that need to be measured and evaluated by construction estimators, it’s time-consuming and labor-intensive.
Fortunately, with a reliable suite of tools for construction project management offering real-time analysis and budgeting updates, estimators can use a construction takeoff process to predict and control materials’ costs and anticipate issues during the process.
Opt for material takeoff and other estimating techniques combined with the best platform designed for construction project managers, estimators, general contractors and everyone involved in the project. Buildern unites the teams and serves as a cloud-based tool to give you an insight into the project’s cost, materials and progress.
Start your journey today and explore Buildern’s features by signing up for a free trial!
Join the thousands of construction companies that use Buildern to save time and money on their projects!