Job Costing in Construction: A Complete Guide to Smarter Project Management
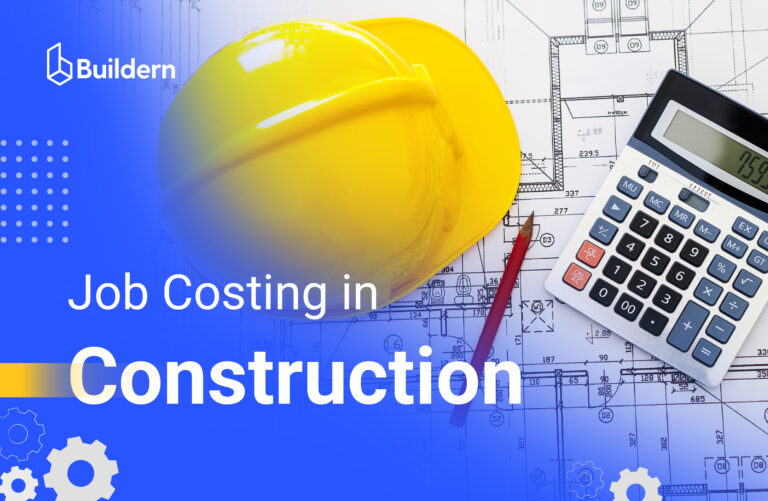
Ever wondered where all the money goes in construction projects? Job costing in construction is the answer to this challenge.
With such a dynamic and complex industry as construction involving countless moving parts, keeping track of so many things can be difficult. This can stem from various factors, including ineffective cash flow management. As a result, projects can get out of control, and expenses can quickly start spiraling. Recent studies revealed that, on average, nationwide construction projects exceed their budget by 16% at a minimum.
Construction job costing serves as an important component of construction accounting, helping companies maximize their profit margin and ensure financial success for every project.
In this article, we will guide you through job costs in construction, explaining what they are and how they can help you ensure the financial stability and health of your construction project.
Table of contents
- What is Job Costing in Construction?
- Job Costing VS Process Costing
- What Should You Include in Construction Job Costing?
- How to Calculate Job Costing
- Common Pain Points in Construction Job Costing
- Benefits of Job Costing
- Tips to Improve Job Costing in Construction
- Bottom Line
TL/DR
- Job costing is the process of calculating all the costs associated with the construction project, ensuring its profitability.
- Job costing is a highly advantageous practice that allows companies to manage budget, track progress, monitor cash flow, and identify issues and track a project’s efficiency.
- Job costing involves tracking and recording all project-related expenses, including labor, materials, and equipment, to ensure accurate financial reporting.
What is Job Costing in Construction
Job costing in construction refers to the process of accurately monitoring costs that are associated with a given construction project. It gives the complete picture of all the costs of your construction project, including labor, materials, equipment, and overheads. With job costing, you can easily track all expenditures and analyze them for future profitability
Additionally, job costing allows you to prevent budget overruns. As you are consistently tracking and managing all the expenses of your construction project, you can identify if it exceeds what you initially budgeted and implement the right measures to rectify the problem.
Job Costing VS Process Costing
Both job costing and process costing are accounting methods that companies utilize to track the cost of their projects. Below, let’s explore each of them individually and see their key differences.
Job costing: Job costing is typical of the construction industry and involves adding the costs for every item, labor, equipment, or overhead. It is usually assigned to a specific construction project. The purpose of job costing is to identify the profitability of the given project.
Process costing: This is typically used in the manufacturing industry and involves adding all costs for long products for the same or similar products. Process costing usually helps companies assess all the costs related to the number of units that are produced. It aims to determine the cost per unit of the material that is used in the production.
What Should You Include in Construction Job Costing?
All the costs that are related to the given construction project should be included in your job costing. Every single detail, starting from managing payrolls to pouring a foundation, should be included. All the expenses associated with construction projects fall into the following overarching categories.
Direct Costs
Direct costs are generally the largest expense for most construction projects. This typically includes labor costs, materials, equipment, and subcontractors. When tracking these costs, it is essential to meticulously pay attention to every detail. In case of labor, you should calculate every working hour or day rates, overtime hours, and any other relevant expenditures. The same applies to the rest of the costs. Precisely calculating these costs can take a lot of time, but utilizing the right software can make all the difference. Using advanced construction estimating software like Buildern, you can track these costs in one place. Utilizing it, you will eliminate manual entries and prevent lost receipts, ensuring accurate job costing throughout the entire project.
Indirect Costs
Indirect costs, also known as soft costs, refer to the non-physical expenses that are associated with the given construction project. Typical indirect costs include project management fees, permits and inspection fees, and legal and accounting fees. These costs are important constituents of construction job costing and can significantly affect a project’s financial viability.
Overhead Costs
Overhead costs make up a substantial proportion of construction projects. It includes administrative fees, insurance costs, vehicles and equipment fees, and marketing and development fees. Accurately calculating overhead costs ensures the financial health and operations of your construction project.
How to Calculate Job Costing?
Job costing is calculated by adding together costs for all the items categorized under the following areas of a project: labor, materials, and overhead. The overall formula for calculating the cost of a job is as follows:
Total Job Cost = Materials + Labor +Subcontractors Costs +Equipment Rental + Permits & Fees + Overheads
Material costs are calculated by summing all raw project materials, such as lumber, steel, and concrete. It also includes material-related costs, such as their delivery to a job site. Labor costs are calculated by multiplying each worker’s day or hourly rate by how long the job takes. Overhead is the cost of doing business and includes administrative fees, advertising and marketing, and insurance premiums, among others.
Example of Job Costing in Construction
Let’s suppose you are building the foundation for a house.
📦 Materials: The total allocated money for all the materials is $15000.
👷Labor: There are three workers, each of them working 8 hours a day, and the hourly rate is $40. In that case, the labor cost will be 3 workers x 10 days x 8 hours x $40 = $9600
🚜Equipment rentals: $4000
📄Permits and Fees: $2500
🏭 Overhead costs: $2000
Job Cost = $15000 + $9600 + $4000 + $2500 + $2000= 33100
Common pain points in construction job costing
Construction is a very challenging industry, and very often companies face several financial problems. Among these problems is companies’ ability to control and track job costing effectively.
Below, let’s discuss a few job costing issues that many construction companies face:
Too many manual processes: A lot of construction companies prefer to do everything manually. While it may be efficient, it causes many downstream problems. This includes delaying proper expense reporting, which can ultimately impede your financial team’s productivity.
Limited real-time visibility: Very often, outdated manual processes can cause limited real-time visibility over your spending. In such scenarios, it becomes challenging to manage your material, labor, or any other associated costs. This, unfortunately, can lead to disruption to your project’s financial management, causing budget overruns.
Lost recipes: It is a common scenario for a construction team to move from one job site to the other. In many cases, unfortunately, they may end up losing the receipt or delaying its submission. As a consequence, it may become challenging to track all the expenses of your construction project.
All of these can be fixed and are achievable if you are using advanced software like Buildern, which can ultimately lead to simple and effective job costing.
Benefits of Construction Job Costing
Construction job costing requires meticulous attention to detail. While it may take a lot of time, it is worth its benefits. Below, let’s explore some of its benefits and see what it helps construction companies to do:
- Manage Budget: Job costing can help you manage the budget of your construction project. As you calculate your job costing and compare it with your estimate, you will immediately see the full picture. You will be able to identify where all your invested money goes and whether it is in line with your budget.
- Track Progress: Job costing can be a powerful tool for tracking your project’s progress. By monitoring milestones and completion rates across different phases of your construction project, you will immediately identify project delays, take the necessary actions, and ensure that your resources are aligned with the current phase.
- Monitor Cash Flow: Construction job costing can help you monitor your cash flow. Precisely tracking all these costs will allow you to see the full picture of your construction project. You will be able to identify when expenses will hit and how much they will be, allowing you to plan your payments efficiently.
- Identify Issues and Track Efficiency: By accurately tracking job costing, you can identify issues easily and track efficiency. As you break down costs by phase or task, you can easily identify where it is falling short and make real-time adjustments. This will ultimately help you reduce costs and ensure that every cent spent contributes to project progress.
Tips to Improve Job Costing in Construction
Below, let’s explore some tips that will help you sharpen your construction job costing process.
- Review cost codes: Cost codes will help you break down your construction project into clear categories. It will help you identify where you allocate your money, compare your actual costs with estimates, and make the necessary adjustments.
- Track and include change orders: It is essential to track and include change orders in your construction projects. If not properly documented, it can lead to inaccurate budget comparisons and distorted profit margins. By incorporating and tracking your change order, you can ensure that your financial data reflects the actual scope of your construction project.
- Track Work in Progress (WIP) Regularly: WIP reports help you align your job costing with project progress. By tracking Work in Progress regularly, you can see whether a project is over- or underbilled and make the necessary adjustments to improve cash flow and your project’s profitability.
- Review projects frequently: It is of utmost importance to monitor job costing and review it throughout the entire project. Double-check to ensure that you have included everything, including overhead costs. This will allow you to make an accurate estimate and make informed decisions in the future.
- Utilize accounting-integrated software for job costing: Using a manual spreadsheet can take a lot of time from you. Therefore, utilizing accounting-integrated software can help you streamline your job costing. Buildern offers Xero and QuickBooks integration, allowing construction companies to connect their project management workflows directly with their accounting system. This ensures that cost data is automatically synced, while minimizing errors and offering real-time visibility to your construction project.
Bottom Line
Construction job costing is more than a mere financial tool: it is a strategic system that gives you full visibility about the financial health of your construction project. It offers a wide suite of benefits, allowing you to see where all your money goes, how it’s spent, and how you can make the necessary improvements. By integrating job costing in your construction projects, you will be able to make informed decisions, reduce financial stress, and have successful construction projects.